With Dana Lim’s newly developed special glue, hospitals can look forward to time savings in the millions as well as significantly safer patient treatment. The new solution keeps tags on the surgical instruments even in tough situations and at the same time complies with the hospitals’ high hygiene standards.
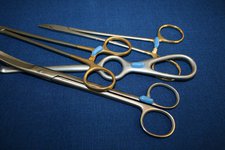
Dana Lim, in collaboration with Rigshospitalet and the company Caretag Surgical, which specializes in the labeling of hospital equipment, has developed a product solution that will help hospitals in connection with the tracking of surgical instruments. The solution is expected to generate major time and financial savings for the hospitals, which annually spend thousands of hours counting instruments before, during and after operations. At the same time, hospitals can look forward to fewer lost instruments, and not least better and significantly safer treatment of patients.
Other producers declined
– The background for Caretag Surgical’s inquiry to us was to develop an integrated solution, which ensures automatic tracking of surgical instruments, so that they can be counted and type determined in a simple and safe way. The solution consists of so-called RFID tags, which are glued to the instruments, i.e. tags, which enable tracking and identification via radio waves. Thereby, the hospital can effectively register which instruments come in and out of which, respectively. operation and cleaning, explains Erik Andersen, who is laboratory manager at Dana Lim.
However, the project offered a number of challenges – not least in connection with the development of the glue that will be used to attach the small tags to the instruments. Several foreign companies specializing in medico products thus tried to deliver an adhesive that could meet the project’s standards in terms of strength, hygiene and non-harmful substances. After several tests of solutions, which proved unable to meet the requirements, Caretag Surgical contacted Dana Lim, who chose to take up the challenge.
Demands out of the ordinary
– The entire toolbox has been used in connection with the development of this special adhesive. The composition of the glue also reflects the hospital world’s strict requirements for safety and hygiene. This is an adhesive that comes into direct contact with the human body during operations, and therefore all of its raw materials have been assessed. On the basis of the latest research, the glue has also been made as future-proof as possible, before it has been submitted for the final biocompatibility test.
In addition to being tough and robust, so that it does not get damaged during use, or if it e.g. is dropped on the floor, the glue’s durability has to meet a number of other requirements, which according to Erik Andersen are far beyond normal. A surgical instrument that has been used is subjected to a rough cleaning process, which removes everything that has stuck – with the exception of the glue. This cleaning is followed by a sterilization process, where the tool is heated to 140 degrees C – a temperature far above the 70-100 degrees C, which is the expected temperature resistance of most glues. At the same time, the glue should protect the RFID tag without reducing the readability of the tag.
Foresight solution
In Dana Lim’s laboratory, high standards, in terms of safety and durability, are far from being idiosyncratic. Nevertheless, in connection with the collaboration with Caretag Surgical and Rigshospitalet, there were disproportionately strict requirements.
– Our solution, which consisted of gluing the used tags, was the only one that the doctors could accept. Likewise, each and every raw material included in the product has been subjected to the most rigorous evaluation. That our product was the only one that ended up passing all the tests, in terms of hygiene, strength and health conditions with cross and snake, is nothing less than a milestone for us, he says and continues:
– Through this project, we have managed to develop a particularly forward-looking solution, which to that extent will pave the way for new product areas. This know-how will benefit other customers, not only in Denmark but worldwide, which has already resulted in several inquiries from new international business partners, he concludes.